Eritme Teknolojisi
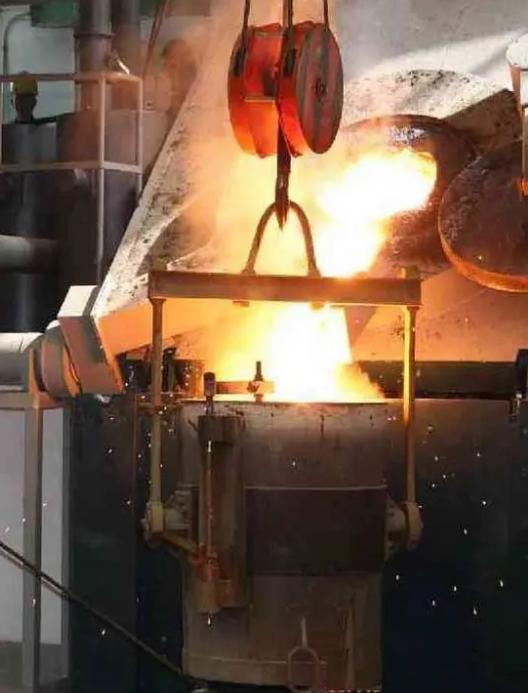
Şu anda, bakır işleme ürünlerinin eritilmesinde genellikle indüksiyonlu eritme fırını benimsenmekte ve aynı zamanda yansımalı fırın eritme ve şaft fırını eritme de benimsenmektedir.
İndüksiyon ocağı ergitme her türlü bakır ve bakır alaşımı için uygundur ve temiz eritme ve eriyik kalitesini garanti etme özelliklerine sahiptir.Fırın yapısına göre indüksiyon fırınları çekirdek indüksiyon fırınları ve çekirdeksiz indüksiyon fırınları olarak ikiye ayrılır.Çekirdekli indüksiyon ocağı, yüksek üretim verimliliği ve yüksek termal verim özelliklerine sahiptir ve kırmızı bakır ve pirinç gibi tek bir bakır ve bakır alaşımı çeşidinin sürekli eritilmesi için uygundur.Çekirdeksiz indüksiyon ocağı, hızlı ısıtma hızı ve alaşım çeşitlerinin kolay değiştirilmesi özelliklerine sahiptir.Bronz, bakır nikel gibi erime noktası yüksek ve çeşitli çeşitleri olan bakır ve bakır alaşımlarının ergitilmesi için uygundur.
Vakum indüksiyon ocağı, elektrikli vakum için oksijensiz bakır, berilyum bronz, zirkonyum bronz, magnezyum bronz vb. gibi solunması ve oksitlenmesi kolay bakır ve bakır alaşımlarının eritilmesine uygun, vakum sistemi ile donatılmış bir indüksiyon ocağıdır.
Yansıtmalı fırın eritme işlemi, eriyikteki yabancı maddeleri rafine edebilir ve çıkarabilir ve esas olarak hurda bakırın eritilmesinde kullanılır.Şaft fırını, yüksek termal verim, yüksek erime hızı ve uygun fırın kapatma avantajlarına sahip bir tür hızlı sürekli eritme fırınıdır.Kontrol edilebilir;herhangi bir arıtma işlemi olmadığından ham maddelerin büyük çoğunluğunun katot bakır olması gerekir.Şaft fırınları genellikle sürekli döküm için sürekli döküm makineleri ile birlikte kullanılır, ayrıca yarı sürekli döküm için bekletme fırınları ile birlikte de kullanılabilir.
Bakır eritme üretim teknolojisinin gelişme eğilimi, esas olarak hammaddelerin yanma kaybını azaltmak, eriyiğin oksidasyonunu ve solunmasını azaltmak, eriyik kalitesini artırmak ve yüksek verimliliği benimsemek (indüksiyon ocağının erime hızı daha yüksektir) şeklinde yansıtılmaktadır. 10 t/saatten fazla), büyük ölçekli (indüksiyon ocağının kapasitesi 35 t/setten fazla olabilir), uzun ömürlü (astar ömrü 1 ila 2 yıldır) ve enerji tasarrufu (indüksiyon ocağının enerji tüketimi) fırın 360 kW h/t'den azdır), tutma fırını bir gaz giderme cihazı (CO gazı gaz giderme) ve indüksiyon ocağı ile donatılmıştır. Sensör sprey yapısını benimser, elektrik kontrol ekipmanı çift yönlü tristör artı frekans dönüşüm güç kaynağını benimser. fırın ön ısıtma, fırın durumu ve refrakter sıcaklık alanı izleme ve alarm sistemi, tutma fırını bir tartım cihazı ile donatılmıştır ve sıcaklık kontrolü daha doğrudur.
Üretim Ekipmanları - Dilme Hattı
Bakır şerit dilme hattının üretimi, geniş bobini açıcı boyunca genişleten, bobini dilme makinesi aracılığıyla gerekli genişliğe kesen ve sarıcı aracılığıyla birkaç bobine geri saran sürekli bir dilme ve dilme üretim hattıdır.(Depolama Rafı) Ruloları depolama rafında depolamak için bir vinç kullanın
↓
(Yükleme arabası) Malzeme rulosunu manuel olarak rulo açıcı tamburuna koymak ve sıkıştırmak için besleme arabasını kullanın
↓
(Bobin açıcı ve gevşeme önleyici baskı rulosu) Açma kılavuzu ve baskı rulosu yardımıyla bobini açın.
↓
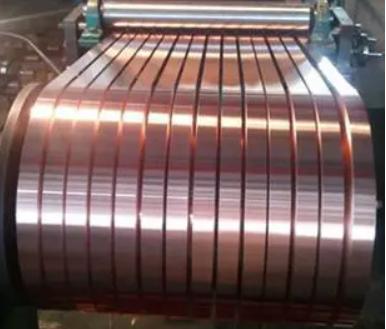
(NO·1 ilmek yapıcı ve döner köprü) depolama ve arabellek
↓
(Kenar kılavuzu ve bastırma silindiri cihazı) Dikey silindirler, sapmayı önlemek için sayfayı sıkıştırma silindirlerine yönlendirir, dikey kılavuz silindirinin genişliği ve konumu ayarlanabilir
↓
(Dilme makinesi) konumlandırma ve dilme için dilme makinesine girin
↓
(Hızlı değiştirilebilir döner koltuk) Takım grubu değişimi
↓
(Hurda sarma cihazı) Hurdayı kesin
↓(Çıkış ucu kılavuz tablası ve bobin kuyruk durdurucusu) NO.2 ilmek yapıcıyı tanıtın
↓
(salınım köprüsü ve NO.2 lüper) malzeme depolama ve kalınlık farkının ortadan kaldırılması
↓
(Baskı plakası gerginliği ve hava genleşme mili ayırma cihazı) gerginlik kuvveti, plaka ve kayış ayırma sağlar
↓
(Dilme makası, direksiyon uzunluğu ölçüm cihazı ve kılavuz tablası) uzunluk ölçümü, bobin sabit uzunluklu segmentasyon, bant diş açma kılavuzu
↓
(sarıcı, ayırma cihazı, itme plakası cihazı) ayırıcı şerit, sarma
↓
(kamyon boşaltma, paketleme) bakır bant boşaltma ve paketleme
Sıcak Haddeleme Teknolojisi
Sıcak haddeleme esas olarak levha, şerit ve folyo üretimi için külçelerin kütük haddelenmesinde kullanılır.
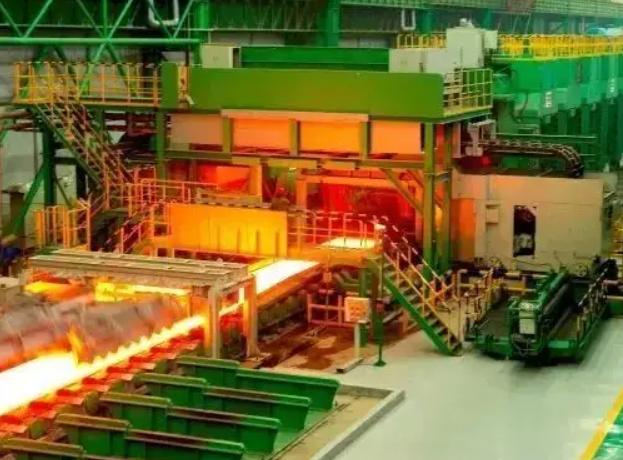
Kütük haddeleme için külçe spesifikasyonları, ürün çeşitliliği, üretim ölçeği, döküm yöntemi vb. faktörleri dikkate almalı ve haddeleme ekipmanı koşullarıyla (rulo açıklığı, rulo çapı, izin verilen haddeleme basıncı, motor gücü ve hadde tablası uzunluğu gibi) ilgili olmalıdır. , vesaire. .Genellikle külçenin kalınlığı ile rulonun çapı arasındaki oran 1: (3,5~7)'dir: genişlik genellikle bitmiş ürünün genişliğine eşit veya birkaç katıdır ve genişlik ve kesme miktarı uygun şekilde ayarlanmalıdır. dikkate alınan.Genellikle levhanın genişliği rulo gövdesinin uzunluğunun %80'i kadar olmalıdır.Külçenin uzunluğu üretim koşullarına göre makul bir şekilde dikkate alınmalıdır.Genel olarak konuşursak, sıcak haddelemenin son haddeleme sıcaklığının kontrol edilebildiği varsayımı altında, külçe ne kadar uzun olursa üretim verimliliği ve verimi de o kadar yüksek olur.
Küçük ve orta ölçekli bakır işleme tesislerinin külçe spesifikasyonları genellikle (60 ~ 150) mm × (220 ~ 450) mm × (2000 ~ 3200) mm'dir ve külçe ağırlığı 1,5 ~ 3 t'dir;büyük bakır işleme tesislerinin külçe özellikleri Genel olarak (150~250)mm×(630~1250)mm×(2400~8000)mm’dir ve külçenin ağırlığı 4,5~20 tondur.
Sıcak haddeleme sırasında, merdanenin yüksek sıcaklıktaki haddeleme parçasıyla temas ettiği anda merdane yüzeyinin sıcaklığı keskin bir şekilde yükselir.Tekrarlanan termal genleşme ve soğuk büzülme, rulo yüzeyinde çatlaklara ve çatlamalara neden olur.Bu nedenle sıcak haddeleme sırasında soğutma ve yağlamanın yapılması gerekir.Soğutma ve yağlama ortamı olarak genellikle su veya daha düşük konsantrasyonlu bir emülsiyon kullanılır.Sıcak haddelemenin toplam çalışma oranı genellikle %90 ila %95 arasındadır.Sıcak haddelenmiş şeridin kalınlığı genellikle 9 ila 16 mm'dir.Sıcak haddelemeden sonra şeridin yüzeyinin frezelenmesi, döküm, ısıtma ve sıcak haddeleme sırasında oluşan yüzey oksit katmanlarını, tufal girintilerini ve diğer yüzey kusurlarını ortadan kaldırabilir.Sıcak haddelenmiş şeridin yüzey kusurlarının ciddiyetine ve prosesin ihtiyaçlarına göre her bir tarafın freze miktarı 0,25 ila 0,5 mm'dir.
Sıcak haddehaneler genellikle iki yüksek veya dört yüksek tersinir haddehanelerdir.Külçenin genişletilmesi ve şerit uzunluğunun sürekli uzatılmasıyla birlikte, sıcak haddehanenin kontrol seviyesi ve işlevi, otomatik kalınlık kontrolü, hidrolik bükme merdanelerinin ön ve arka kullanımı gibi sürekli bir iyileştirme ve iyileştirme eğilimine sahiptir. dikey rulolar, sadece soğutma olmadan ruloları soğutma Haddeleme cihazı cihazı, TP rulo (Konik Piston Rulo) taç kontrolü, haddelemeden sonra çevrimiçi söndürme (söndürme), çevrimiçi sarma ve şerit yapısının ve özelliklerinin tekdüzeliğini geliştirmek ve daha iyi elde etmek için diğer teknolojiler plaka.
Döküm Teknolojisi
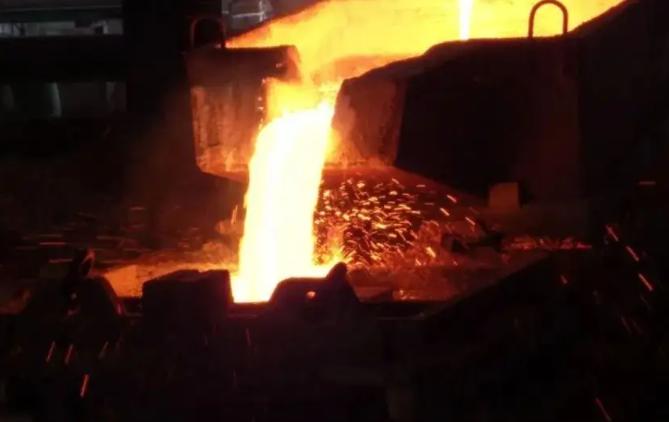
Bakır ve bakır alaşımlarının dökümü genel olarak şu şekilde ayrılır: dikey yarı sürekli döküm, dikey tam sürekli döküm, yatay sürekli döküm, yukarı doğru sürekli döküm ve diğer döküm teknolojileri.
A. Dikey Yarı Sürekli Döküm
Dikey yarı sürekli döküm, basit ekipman ve esnek üretim özelliklerine sahiptir ve çeşitli yuvarlak ve düz bakır ve bakır alaşımları külçelerinin dökümü için uygundur.Dikey yarı sürekli döküm makinesinin iletim modu hidrolik, kurşun vida ve tel halata bölünmüştür.Hidrolik şanzıman nispeten stabil olduğundan daha fazla kullanılmaktadır.Kristalleştirici gerektiği gibi farklı genlik ve frekanslarda titreştirilebilir.Günümüzde bakır ve bakır alaşımlı külçelerin üretiminde yarı sürekli döküm yöntemi yaygın olarak kullanılmaktadır.
B. Dikey tam Sürekli Döküm
Dikey tam sürekli döküm, büyük üretim ve yüksek verim (yaklaşık %98) özelliklerine sahiptir, tek çeşit ve spesifikasyonla büyük ölçekli ve sürekli külçe üretimi için uygundur ve eritme ve döküm için ana seçim yöntemlerinden biri haline gelmektedir. Modern büyük ölçekli bakır şerit üretim hatlarında süreç.Dikey tam sürekli döküm kalıbı, temassız lazer sıvı seviyesi otomatik kontrolünü benimser.Döküm makinesi genellikle hidrolik sıkma, mekanik şanzıman, çevrimiçi yağ soğutmalı kuru talaş kesme ve talaş toplama, otomatik işaretleme ve külçeyi eğme işlemlerini benimser.Yapı karmaşıktır ve otomasyon derecesi yüksektir.
C. Yatay Sürekli Döküm
Yatay sürekli döküm kütük ve tel kütük üretebilir.
Şerit yatay sürekli döküm, 14-20 mm kalınlığında bakır ve bakır alaşımlı şeritler üretebilir.Bu kalınlık aralığındaki şeritler, sıcak haddeleme olmadan doğrudan soğuk haddelenebilir, bu nedenle genellikle sıcak haddelenmesi zor olan alaşımların (kalay, fosfor bronz, kurşun pirinç vb.) üretilmesinde kullanılırlar, aynı zamanda pirinç de üretebilirler, cupronickel ve düşük alaşımlı bakır alaşımlı şerit.Döküm şeridinin genişliğine bağlı olarak yatay sürekli dökümde aynı anda 1 ila 4 şerit dökülebilir.Yaygın olarak kullanılan yatay sürekli döküm makineleri, her biri 450 mm'den az genişliğe sahip iki şeridi aynı anda dökebilir veya 650-900 mm şerit genişliğine sahip bir şeridi aynı anda dökebilir.Yatay sürekli döküm şeridi genellikle çekme-durdurma-geri itme döküm işlemini benimser ve yüzeyde genellikle frezeleme ile ortadan kaldırılması gereken periyodik kristalizasyon çizgileri bulunur.Şerit kütüklerin frezelemeden çekilmesi ve dökülmesiyle üretilebilen yüksek yüzeyli bakır şeritlerin yerli örnekleri vardır.
Boru, çubuk ve tel kütüklerin yatay sürekli dökümü, farklı alaşımlara ve özelliklere göre aynı anda 1 ila 20 külçe dökebilir.Genellikle çubuğun veya ham telin çapı 6 ila 400 mm'dir ve ham tüpün dış çapı 25 ila 300 mm'dir.Duvar kalınlığı 5-50 mm, külçenin yan uzunluğu 20-300 mm'dir.Yatay sürekli döküm yönteminin avantajları prosesin kısa olması, imalat maliyetinin düşük olması ve üretim verimliliğinin yüksek olmasıdır.Aynı zamanda sıcak işlenebilirliği zayıf olan bazı alaşımlı malzemeler için de gerekli bir üretim yöntemidir.Son zamanlarda, kalay-fosfor bronz şeritler, çinko-nikel alaşımlı şeritler ve fosforla oksitlenmemiş bakır klima boruları gibi yaygın olarak kullanılan bakır ürünlerin kütüklerinin yapımında ana yöntemdir.Üretim yöntemleri.
Yatay sürekli döküm üretim yönteminin dezavantajları şunlardır: uygun alaşım çeşitleri nispeten basittir, kalıbın iç kovanındaki grafit malzemenin tüketimi nispeten büyüktür ve külçenin enine kesitinin kristal yapısının tekdüzeliği değildir. kontrolü kolaydır.Kalıbın iç duvarına yakın olan külçenin alt kısmı yer çekiminin etkisiyle sürekli olarak soğutulur ve taneler daha ince olur;üst kısım hava boşluklarının oluşmasından ve yüksek erime sıcaklığından kaynaklanır, bu da külçenin katılaşmasında gecikmeye neden olur, bu da soğuma hızını yavaşlatır ve külçe katılaşma histerezisine neden olur.Kristalin yapı nispeten kabadır ve bu özellikle büyük boyutlu külçeler için belirgindir.Yukarıdaki eksiklikler göz önüne alındığında, kütük ile dikey bükerek döküm yöntemi şu anda geliştirilmektedir.Bir Alman şirketi, DHP ve CuSn6 gibi (16-18) mm × 680 mm kalay bronz şeritlerin 600 mm/dak hızla test dökümü için dikey bükme sürekli döküm makinesi kullandı.
D. Yukarıya Doğru Sürekli Döküm
Yukarı doğru sürekli döküm, son 20-30 yılda hızla gelişen ve parlak bakır filmaşinler için kütük üretiminde yaygın olarak kullanılan bir döküm teknolojisidir.Vakum emmeli döküm prensibini kullanır ve sürekli çok kafalı dökümü gerçekleştirmek için stop-pull teknolojisini kullanır.Basit ekipman, küçük yatırım, daha az metal kaybı ve düşük çevre kirliliği prosedürleri özelliklerine sahiptir.Yukarıya doğru sürekli döküm genellikle kırmızı bakır ve oksijensiz bakır tel kütüklerin üretimi için uygundur.Son yıllarda geliştirilen yeni başarı, geniş çaplı boru boşluklarında, pirinçte ve bakır nikelde yaygınlaştırılması ve uygulanmasıdır.Şu anda, yıllık üretimi 5.000 ton ve çapı Φ100 mm'den fazla olan bir yukarı doğru sürekli döküm ünitesi geliştirilmiştir;ikili sıradan pirinç ve çinko-beyaz bakır üçlü alaşımlı tel kütükler üretildi ve tel kütüklerin verimi% 90'ın üzerine çıkabiliyor.
E. Diğer Döküm Teknikleri
Sürekli döküm kütük teknolojisi geliştirilme aşamasındadır.Yukarıya doğru sürekli dökümün stop-pull işlemi nedeniyle kütük dış yüzeyinde oluşan şantuk izi gibi kusurları giderir ve yüzey kalitesi mükemmeldir.Neredeyse yönlü katılaşma özellikleri nedeniyle iç yapı daha düzgün ve saftır, dolayısıyla ürünün performansı da daha iyidir.Bant tipi sürekli döküm bakır tel kütük üretim teknolojisi, 3 tonun üzerindeki büyük üretim hatlarında yaygın olarak kullanılmaktadır.Levhanın kesit alanı genellikle 2000 mm2'den fazladır ve bunu yüksek üretim verimliliğine sahip sürekli bir haddehane takip eder.
Elektromanyetik döküm ülkemizde 1970'li yılların başlarında denenmiş ancak endüstriyel üretim gerçekleştirilememiştir.Son yıllarda elektromanyetik döküm teknolojisi büyük ilerleme kaydetti.Şu anda, Φ200 mm'lik oksijensiz bakır külçeler pürüzsüz yüzeyli olarak başarıyla dökülmektedir.Aynı zamanda, elektromanyetik alanın eriyik üzerindeki karıştırma etkisi, egzozun ve cürufun uzaklaştırılmasını destekleyebilir ve %0,001'den daha az oksijen içeriğine sahip oksijensiz bakır elde edilebilir.
Yeni bakır alaşımlı döküm teknolojisinin yönü, katılaşma teorisine göre yönlü katılaşma, hızlı katılaşma, yarı katı şekillendirme, elektromanyetik karıştırma, metamorfik işlem, sıvı seviyesinin otomatik kontrolü ve diğer teknik araçlar yoluyla kalıbın yapısını iyileştirmektir., yoğunlaştırma, saflaştırma ve sürekli çalışmayı ve yakın uç şekillendirmeyi gerçekleştirir.
Uzun vadede, bakır ve bakır alaşımlarının dökümü, yarı sürekli döküm teknolojisi ile tam sürekli döküm teknolojisinin bir arada bulunması anlamına gelecek ve sürekli döküm teknolojisinin uygulama oranı artmaya devam edecektir.
Soğuk Haddeleme Teknolojisi
Haddelenmiş şerit spesifikasyonuna ve haddeleme işlemine göre, soğuk haddeleme; açma, ara haddeleme ve son haddeleme olarak alt bölümlere ayrılır.14 ila 16 mm kalınlığındaki döküm şeridin ve yaklaşık 5 ila 16 mm ila 2 ila 6 mm kalınlığındaki sıcak haddelenmiş kütüğün soğuk haddelenmesi işlemine çiçeklenme adı verilir ve kalınlığın azaltılmaya devam edilmesi işlemine, haddelenmiş parçaya ara haddeleme denir.Bitmiş ürünün gereksinimlerini karşılamak için yapılan son soğuk haddelemeye son haddeleme denir.
Soğuk haddeleme işleminin, farklı alaşımlara, haddeleme özelliklerine ve bitmiş ürün performans gereksinimlerine göre indirgeme sistemini (toplam işleme hızı, geçiş işleme hızı ve bitmiş ürün işleme hızı) kontrol etmesi, rulo şeklini makul bir şekilde seçip ayarlaması ve yağlamayı makul bir şekilde seçmesi gerekir. Yöntem ve yağlayıcı.Gerginlik ölçümü ve ayarı.
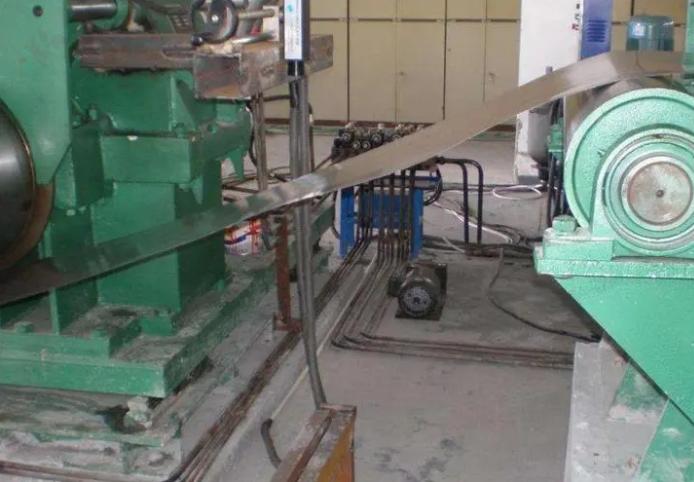
Soğuk haddehaneler genellikle dört yüksek veya çok yüksek tersinir haddehaneler kullanır.Modern soğuk haddehaneler genellikle hidrolik pozitif ve negatif hadde bükme, otomatik kalınlık, basınç ve gerilim kontrolü, merdanelerin eksenel hareketi, merdanelerin bölümsel soğutulması, plaka şeklinin otomatik kontrolü ve haddelenmiş parçaların otomatik hizalanması gibi bir dizi teknoloji kullanır. Böylece şeridin doğruluğu geliştirilebilir.0,25±0,005 mm'ye kadar ve plaka şeklinin 5I dahilinde.
Soğuk haddeleme teknolojisinin gelişme eğilimi, yüksek hassasiyetli çok silindirli haddelerin, daha yüksek haddeleme hızlarının, daha doğru şerit kalınlığı ve şekil kontrolünün ve soğutma, yağlama, sarma, merkezleme ve hızlı haddeleme gibi yardımcı teknolojilerin geliştirilmesi ve uygulanmasına yansır. değiştirmek.arıtma vb.
Üretim Ekipmanları-Çan Ocağı
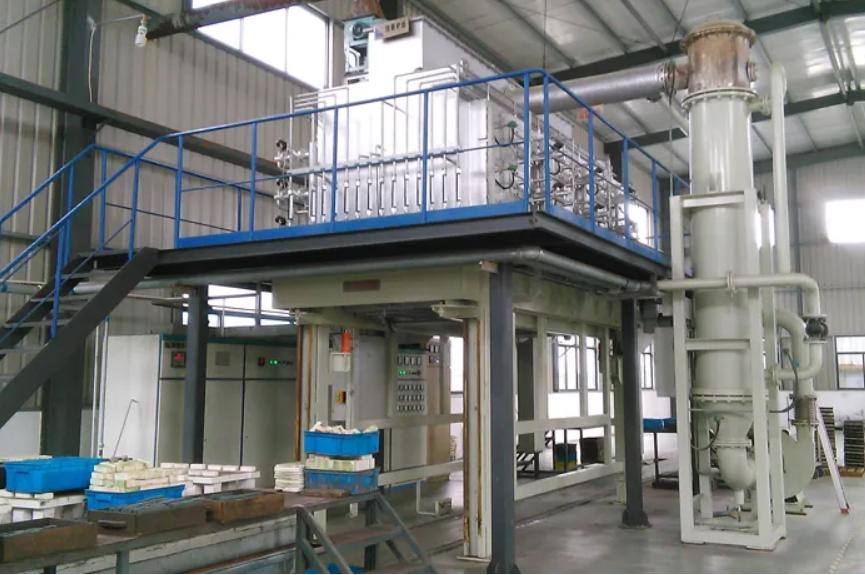
Çan kavanoz fırınları ve kaldırma fırınları genellikle endüstriyel üretimde ve pilot testlerde kullanılmaktadır.Genellikle güç büyüktür ve güç tüketimi büyüktür.Endüstriyel işletmeler için Luoyang Sigma kaldırma fırınının fırın malzemesi, iyi enerji tasarrufu etkisine, düşük enerji tüketimine ve düşük enerji tüketimine sahip olan seramik elyaftır.Üretimi artırmak için faydalı olan elektrik ve zamandan tasarruf edin.
Yirmi beş yıl önce, Alman BRANDS ve ferrit imalat sektörünün önde gelen şirketlerinden Philips, ortaklaşa yeni bir sinterleme makinesi geliştirdi.Bu ekipmanın geliştirilmesi ferrit endüstrisinin özel ihtiyaçlarını karşılamaktadır.Bu süreçte MARKALAR Çan Ocağı sürekli olarak güncellenmektedir.
MARKALARIN yüksek kaliteli ekipmanlarından da büyük fayda sağlayan Philips, Siemens, TDK, FDK gibi dünyaca ünlü firmaların ihtiyaçlarına önem veriyor.
Çan fırınları tarafından üretilen ürünlerin yüksek stabilitesi nedeniyle, çan fırınları profesyonel ferrit üretim sektörünün en iyi firmaları haline gelmiştir.Yirmi beş yıl önce BRANDS tarafından üretilen ilk fırın, hâlâ Philips için yüksek kaliteli ürünler üretiyor.
Çan fırınının sunduğu sinterleme fırınının temel özelliği yüksek verimliliğidir.Akıllı kontrol sistemi ve diğer ekipmanları, ferrit endüstrisinin neredeyse en son teknoloji gereksinimlerini tam olarak karşılayabilen eksiksiz bir işlevsel ünite oluşturur.
Çan kavanoz fırını müşterileri, yüksek kaliteli ürünler üretmek için gereken her türlü sıcaklık/atmosfer profilini programlayabilir ve saklayabilir.Ayrıca müşteriler gerçek ihtiyaçlara göre diğer ürünleri de zamanında üretebilir, böylece teslimat süreleri kısalır ve maliyetler düşer.Sinterleme ekipmanı, pazarın ihtiyaçlarına sürekli olarak uyum sağlamak amacıyla çeşitli farklı ürünler üretebilmek için iyi ayarlanabilirliğe sahip olmalıdır.Bu, ilgili ürünlerin bireysel müşterinin ihtiyaçlarına göre üretilmesi gerektiği anlamına gelir.
İyi bir ferrit üreticisi, müşterilerinin özel ihtiyaçlarını karşılamak için 1000'den fazla farklı mıknatıs üretebilir.Bunlar, sinterleme işleminin yüksek hassasiyetle tekrarlanabilmesini gerektirir.Çan kavanoz fırın sistemleri tüm ferrit üreticileri için standart fırın haline gelmiştir.
Ferrit endüstrisinde bu fırınlar, özellikle iletişim endüstrisinde düşük güç tüketimi ve yüksek μ değeri olan ferrit için kullanılır.Çan fırını olmadan yüksek kalitede maça üretmek mümkün değildir.
Çan fırını, sinterleme sırasında yalnızca birkaç operatöre ihtiyaç duyar, yükleme ve boşaltma gün boyunca tamamlanabilir ve sinterleme gece tamamlanabilir, bu da günümüzün elektrik kesintisi durumunda çok pratik olan elektriğin en yüksek düzeyde tıraşlanmasını sağlar.Çan kavanoz fırınları yüksek kaliteli ürünler üretir ve tüm ek yatırımlar, yüksek kaliteli ürünler sayesinde hızla geri döner.Sıcaklık ve atmosfer kontrolü, fırın tasarımı ve fırın içindeki hava akışı kontrolü, ürünün eşit şekilde ısıtılmasını ve soğutulmasını sağlamak için mükemmel şekilde entegre edilmiştir.Soğutma sırasında fırın atmosferinin kontrolü doğrudan fırın sıcaklığıyla ilgilidir ve %0,005 veya daha düşük bir oksijen içeriğini garanti edebilir.Bunlar rakiplerimizin yapamayacağı şeyler.
Eksiksiz alfanümerik programlama giriş sistemi sayesinde uzun sinterleme işlemleri kolayca kopyalanabilir, böylece ürün kalitesi sağlanır.Bir ürünü satarken aynı zamanda ürünün kalitesinin de bir yansımasıdır.
Isıl İşlem Teknolojisi
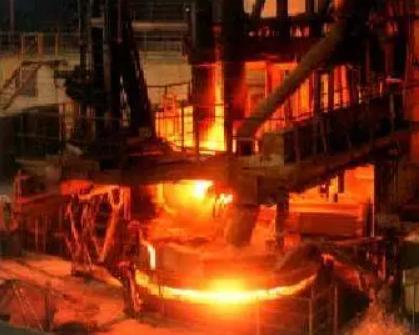
Kalay-fosfor bronz gibi ciddi dendrit ayrışması veya döküm gerilimine sahip birkaç alaşım külçesinin (şeritlerinin), genellikle bir fanus fırınında gerçekleştirilen özel homojenizasyon tavlamasına tabi tutulması gerekir.Homojenizasyon tavlama sıcaklığı genellikle 600 ila 750°C arasındadır.
Şu anda, bakır alaşımlı şeritlerin ara tavlamasının (yeniden kristalleştirme tavlaması) ve bitmiş tavlamasının (ürünün durumunu ve performansını kontrol etmek için tavlama) çoğu, gaz korumasıyla parlak tavlamadır.Fırın türleri arasında fanus fırını, hava yastıklı fırın, dikey çekişli fırın vb. yer almaktadır. Oksidatif tavlama aşamalı olarak kaldırılmaktadır.
Isıl işlem teknolojisinin gelişme eğilimi, çökeltmeyle güçlendirilmiş alaşım malzemelerin sıcak haddeleme çevrimiçi çözüm işlemine ve ardından deformasyon ısıl işlem teknolojisine, sürekli parlak tavlamaya ve koruyucu bir atmosferde gerilim tavlamasına yansır.
Söndürme - Yaşlandırma ısıl işlemi esas olarak bakır alaşımlarının ısıl işlemle güçlendirilmesi için kullanılır.Isıl işlem sayesinde ürün mikro yapısını değiştirerek gerekli özel özellikleri kazanır.Yüksek mukavemetli ve iletkenliği yüksek alaşımların gelişmesiyle birlikte su verme-yaşlandırma ısıl işlemi daha çok uygulanacaktır.Yaşlandırma arıtma ekipmanı kabaca tavlama ekipmanıyla aynıdır.
Ekstrüzyon Teknolojisi
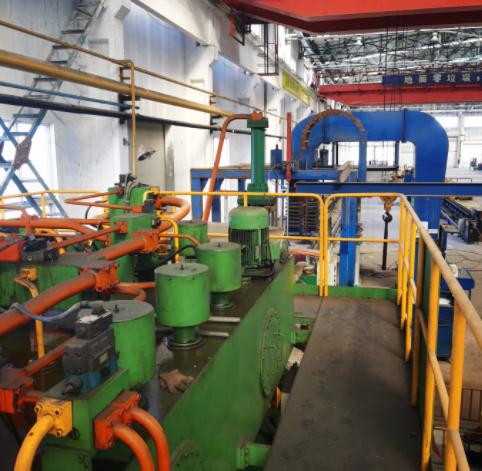
Ekstrüzyon, olgun ve gelişmiş bir bakır ve bakır alaşımlı boru, çubuk, profil üretimi ve kütük tedarik yöntemidir.Kalıbı değiştirerek veya delikli ekstrüzyon yöntemini kullanarak çeşitli alaşım çeşitleri ve farklı kesit şekilleri doğrudan ekstrüde edilebilir.Ekstrüzyon yoluyla külçenin döküm yapısı işlenmiş bir yapıya dönüştürülür ve ekstrüde edilmiş boru kütüğü ve çubuk kütüğü yüksek boyutsal doğruluğa sahiptir ve yapı ince ve düzgündür.Ekstrüzyon yöntemi yerli ve yabancı bakır boru ve çubuk üreticilerinin yaygın olarak kullandığı bir üretim yöntemidir.
Bakır alaşımlı dövme, ülkemdeki ağırlıklı olarak makine üreticileri tarafından gerçekleştirilmekte olup, esas olarak büyük dişliler, sonsuz dişliler, sonsuz dişliler, otomobil senkronizatör dişli halkaları vb. gibi serbest dövme ve kalıpta dövme dahil olmak üzere yapılmaktadır.
Ekstrüzyon yöntemi üç tipe ayrılabilir: ileri ekstrüzyon, ters ekstrüzyon ve özel ekstrüzyon.Bunlar arasında ileri ekstrüzyonun birçok uygulaması vardır, küçük ve orta boy çubuk ve tellerin üretiminde ters ekstrüzyon kullanılır, özel üretimde özel ekstrüzyon kullanılır.
Ekstrüzyon sırasında, alaşımın özelliklerine, ekstrüde edilen ürünlerin teknik gereksinimlerine ve ekstrüderin kapasitesi ve yapısına göre külçenin türü, boyutu ve ekstrüzyon katsayısı makul bir şekilde seçilmelidir, böylece deformasyon derecesi %85'ten az değil.Ekstrüzyon sıcaklığı ve ekstrüzyon hızı, ekstrüzyon işleminin temel parametreleridir ve makul ekstrüzyon sıcaklık aralığı, metalin plastisite diyagramına ve faz diyagramına göre belirlenmelidir.Bakır ve bakır alaşımları için ekstrüzyon sıcaklığı genellikle 570 ila 950 °C arasındadır ve bakırdan ekstrüzyon sıcaklığı 1000 ila 1050 °C kadar yüksektir.400 ila 450 °C arasındaki ekstrüzyon silindiri ısıtma sıcaklığıyla karşılaştırıldığında, ikisi arasındaki sıcaklık farkı nispeten yüksektir.Ekstrüzyon hızı çok yavaşsa, külçe yüzeyinin sıcaklığı çok hızlı düşecek ve bu da metal akışının düzensizliğinde bir artışa neden olacak, bu da ekstrüzyon yükünün artmasına ve hatta delme olayına neden olacaktır. .Bu nedenle, bakır ve bakır alaşımları genellikle nispeten yüksek hızlı ekstrüzyon kullanır, ekstrüzyon hızı 50 mm/s'den fazla olabilir.
Bakır ve bakır alaşımları ekstrüde edildiğinde, külçenin yüzey kusurlarını gidermek için genellikle soyma ekstrüzyonu kullanılır ve soyma kalınlığı 1-2 m'dir.Ekstrüzyon kütüğünün çıkışında genellikle su yalıtımı kullanılır, böylece ürün ekstrüzyondan sonra su tankında soğutulabilir ve ürün yüzeyi oksitlenmez ve ardından dekapaj olmadan soğuk işlem gerçekleştirilebilir.Üretim verimliliğini ve sonraki sekansın kapsamlı verimini etkili bir şekilde artırmak amacıyla, tek ağırlığı 500 kg'dan fazla olan tüp veya tel bobinleri ekstrüde etmek için senkronize bir toplama cihazına sahip büyük tonajlı bir ekstrüder kullanma eğilimindedir.Şu anda, bakır ve bakır alaşımlı boruların üretiminde çoğunlukla bağımsız perforasyon sistemine (çift etkili) ve doğrudan yağ pompası aktarımına sahip yatay hidrolik ileri ekstrüderler kullanılmaktadır ve çubukların üretiminde çoğunlukla bağımsız olmayan perforasyon sistemi (tek etkili) ve yağ pompası doğrudan şanzıman.Yatay hidrolik ileri veya geri ekstruder.Yaygın olarak kullanılan ekstruder spesifikasyonları 8-50 MN'dir ve artık külçenin tek ağırlığını artırmak, böylece üretim verimliliğini ve verimi artırmak için 40 MN'nin üzerindeki büyük tonajlı ekstrüderler tarafından üretilme eğilimindedir.
Modern yatay hidrolik ekstruderler yapısal olarak öngerilmeli entegre çerçeve, ekstrüzyon namlusu "X" kılavuzu ve desteği, yerleşik delik açma sistemi, delikli iğne dahili soğutması, kayan veya döner kalıp seti ve hızlı Kalıp değiştirme cihazı, yüksek güçlü değişken yağ pompası doğrudan ile donatılmıştır. sürücü, entegre mantıksal valf, PLC kontrolü ve diğer ileri teknolojiler, ekipmanın yüksek hassasiyeti, kompakt yapısı, kararlı çalışması, güvenli kilitleme ve program kontrolünü gerçekleştirmesi kolaydır.Sürekli ekstrüzyon (Conform) teknolojisi, özellikle elektrikli lokomotif telleri gibi özel şekilli çubukların üretimi için son on yılda bir miktar ilerleme kaydetmiştir ve bu oldukça umut vericidir.Son yıllarda, yeni ekstrüzyon teknolojisi hızla gelişti ve ekstrüzyon teknolojisinin gelişme eğilimi şu şekilde şekillendi: (1) Ekstrüzyon ekipmanı.Ekstrüzyon presinin ekstrüzyon kuvveti daha büyük bir yönde gelişecek ve 30MN'den fazla ekstrüzyon presi ana gövde haline gelecek ve ekstrüzyon presi üretim hattının otomasyonu gelişmeye devam edecektir.Modern ekstrüzyon makineleri, bilgisayar programı kontrolünü ve programlanabilir mantık kontrolünü tamamen benimsemiştir, böylece üretim verimliliği büyük ölçüde artar, operatörler önemli ölçüde azalır ve hatta ekstrüzyon üretim hatlarının otomatik insansız çalışmasını gerçekleştirmek bile mümkündür.
Ekstruderin gövde yapısı da sürekli olarak geliştirilmiş ve mükemmelleştirilmiştir.Son yıllarda bazı yatay ekstrüderler genel yapının stabilitesini sağlamak için öngerilmeli bir çerçeveyi benimsemiştir.Modern ekstrüder ileri ve geri ekstrüzyon yöntemlerini gerçekleştirir.Ekstruder iki ekstrüzyon şaftı (ana ekstrüzyon şaftı ve kalıp şaftı) ile donatılmıştır.Ekstrüzyon sırasında ekstrüzyon silindiri ana mil ile birlikte hareket eder.Bu sırada ürün çıkış yönü ana şaftın hareket yönü ile tutarlıdır ve kalıp ekseninin göreceli hareket yönünün tersidir.Ekstruderin kalıp tabanı aynı zamanda birden fazla istasyonun konfigürasyonunu da benimser; bu, yalnızca kalıp değişimini kolaylaştırmakla kalmaz, aynı zamanda üretim verimliliğini de artırır.Modern ekstrüderler, zamanında ve hızlı ayarlama için uygun olan, ekstrüzyon merkez hattının durumu hakkında etkili veriler sağlayan bir lazer sapma ayar kontrol cihazı kullanır.Çalışma ortamı olarak yağı kullanan yüksek basınçlı pompa doğrudan tahrikli hidrolik pres, hidrolik presin yerini tamamen almıştır.Ekstrüzyon araçları da ekstrüzyon teknolojisinin gelişmesiyle birlikte sürekli olarak güncellenmektedir.Dahili su soğutmalı delme iğnesi geniş çapta tanıtılmıştır ve değişken kesitli delme ve yuvarlanma iğnesi, yağlama etkisini büyük ölçüde artırır.Daha uzun ömürlü ve yüzey kalitesi daha yüksek olan seramik kalıplar ve alaşımlı çelik kalıplar daha yaygın olarak kullanılmaktadır.
Ekstrüzyon araçları da ekstrüzyon teknolojisinin gelişmesiyle birlikte sürekli olarak güncellenmektedir.Dahili su soğutmalı delme iğnesi geniş çapta tanıtılmıştır ve değişken kesitli delme ve yuvarlanma iğnesi, yağlama etkisini büyük ölçüde artırır.Daha uzun ömürlü ve yüzey kalitesi daha yüksek olan seramik kalıpların ve alaşımlı çelik kalıpların uygulaması daha popüler hale gelmektedir.(2) Ekstrüzyon üretim süreci.Ekstrüde ürünlerin çeşitleri ve özellikleri sürekli genişlemektedir.Küçük kesitli, ultra yüksek hassasiyetli tüplerin, çubukların, profillerin ve süper büyük profillerin ekstrüzyonu, ürünlerin görünüm kalitesini garanti eder, ürünlerin iç kusurlarını azaltır, geometrik kaybı azaltır ve ayrıca ekstrüde edilmiş malzemelerin tekdüze performansı gibi ekstrüzyon yöntemlerini destekler. ürünler.Modern ters ekstrüzyon teknolojisi de yaygın olarak kullanılmaktadır.Kolayca oksitlenen metaller için, dekapaj kirliliğini azaltabilen, metal kaybını azaltabilen ve ürünlerin yüzey kalitesini artırabilen su contalı ekstrüzyon benimsenmiştir.Söndürülmesi gereken ekstrüde ürünler için sadece uygun sıcaklığı kontrol etmeniz yeterlidir.Su contası ekstrüzyon yöntemi amaca ulaşabilir, üretim döngüsünü etkili bir şekilde kısaltabilir ve enerji tasarrufu sağlayabilir.
Ekstrüder kapasitesinin ve ekstrüzyon teknolojisinin sürekli gelişmesiyle birlikte, izotermal ekstrüzyon, soğutma kalıp ekstrüzyonu, yüksek hızlı ekstrüzyon ve diğer ileri ekstrüzyon teknolojileri, ters ekstrüzyon, hidrostatik ekstrüzyon gibi modern ekstrüzyon teknolojisi yavaş yavaş uygulanmıştır. Sürekli ekstrüzyon teknolojisinin pratik uygulaması presleme ve Conform, düşük sıcaklıktaki süper iletken malzemelerin toz ekstrüzyon ve katmanlı kompozit ekstrüzyon teknolojisinin uygulanması, yarı katı metal ekstrüzyon ve çok boşluklu ekstrüzyon gibi yeni yöntemlerin geliştirilmesi, küçük hassas parçaların geliştirilmesi Soğuk ekstrüzyon şekillendirme teknolojisi, vb. hızla geliştirildi ve yaygın olarak geliştirildi ve uygulandı.
Spektrometre
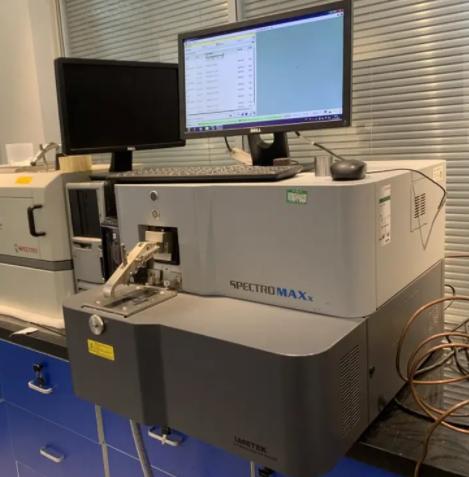
Spektroskop, karmaşık bileşime sahip ışığı spektral çizgilere ayrıştıran bilimsel bir araçtır.Güneş ışığındaki yedi renkli ışık, çıplak gözün ayırt edebildiği kısımdır (görünür ışık), ancak güneş ışığı bir spektrometre tarafından ayrıştırılır ve dalga boyuna göre düzenlenirse görünür ışık, spektrumda yalnızca küçük bir aralıkta yer alır ve geri kalanı gölgede kalır. Kızılötesi ışınlar, mikrodalgalar, UV ışınları, X ışınları vb. gibi çıplak gözle ayırt edilemeyen spektrumlar. Optik bilgi, spektrometre tarafından yakalanır, bir fotoğraf filmiyle geliştirilir veya bilgisayarlı bir otomatik ekran tarafından görüntülenip analiz edilir. Makalede hangi unsurların bulunduğunu tespit etmek için sayısal bir araç.Bu teknoloji, hava kirliliği, su kirliliği, gıda hijyeni, metal endüstrisi vb. tespitinde yaygın olarak kullanılmaktadır.
Spektrometre olarak da bilinen spektrometre, yaygın olarak doğrudan okumalı spektrometre olarak bilinir.Fotoçoğaltıcı tüpler gibi fotodetektörlerle farklı dalga boylarındaki spektral çizgilerin yoğunluğunu ölçen bir cihaz.Bir giriş yarığından, bir dağıtıcı sistemden, bir görüntüleme sisteminden ve bir veya daha fazla çıkış yarığından oluşur.Radyasyon kaynağının elektromanyetik radyasyonu, dağıtıcı eleman tarafından gerekli dalga boyu veya dalga boyu bölgesine ayrılır ve seçilen dalga boyunda (veya belirli bir bandı tarayarak) yoğunluk ölçülür.İki tip monokromatör ve polikromatör vardır.
Test Cihazı-İletkenlik Ölçer
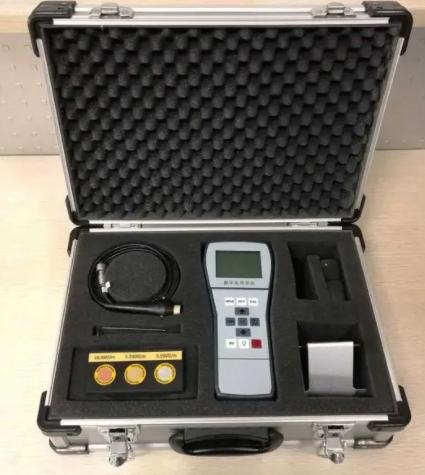
Dijital el tipi metal iletkenlik test cihazı (iletkenlik ölçer) FD-101, girdap akımı algılama prensibini uygular ve elektrik endüstrisinin iletkenlik gereksinimlerine göre özel olarak tasarlanmıştır.İşlevsellik ve doğruluk açısından metal sektörünün test standartlarını karşılamaktadır.
1. Girdap akımı iletkenlik ölçer FD-101'in üç benzersiz özelliği vardır:
1) Havacılık Malzemeleri Enstitüsü'nün doğrulamasını geçen tek Çin iletkenlik ölçer;
2) Uçak endüstrisi şirketlerinin ihtiyaçlarını karşılayabilecek tek Çin iletkenlik ölçer;
3) Birçok ülkeye ihraç edilen tek Çin iletkenlik ölçer.
2. Ürün fonksiyonu tanıtımı:
1) Geniş ölçüm aralığı: Tüm demir dışı metallerin iletkenlik testini karşılayan %6,9 IACS-%110 IACS(4,0MS/m-64MS/m).
2) Akıllı kalibrasyon: hızlı ve doğru, manuel kalibrasyon hatalarından tamamen kaçınır.
3) Cihaz iyi bir sıcaklık telafisine sahiptir: okuma 20 °C'deki değere otomatik olarak telafi edilir ve düzeltme insan hatasından etkilenmez.
4) İyi stabilite: kalite kontrol için kişisel korumanızdır.
5) İnsancıllaştırılmış akıllı yazılım: Size rahat bir algılama arayüzü ve güçlü veri işleme ve toplama fonksiyonları sunar.
6) Rahat kullanım: Üretim alanı ve laboratuvar her yerde kullanılabilir ve kullanıcıların çoğunluğunun beğenisini kazanır.
7) Probların kendi kendine değiştirilmesi: Her ana bilgisayar birden fazla probla donatılabilir ve kullanıcılar bunları istedikleri zaman değiştirebilir.
8) Sayısal çözünürlük: %0,1 IACS (MS/m)
9) Ölçüm arayüzü, ölçüm değerlerini aynı anda iki birim %IACS ve MS/m cinsinden görüntüler.
10) Ölçüm verilerini tutma işlevi vardır.
Sertlik ölçme aleti
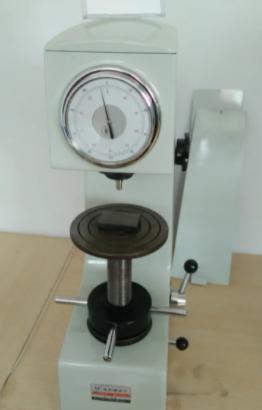
Cihaz, girintili görüntülemeyi daha net ve ölçümü daha doğru hale getiren mekanik, optik ve ışık kaynağı açısından benzersiz ve hassas bir tasarıma sahiptir.Hem 20x hem de 40x objektif lensler ölçüme katılarak ölçüm aralığını genişletir ve uygulamayı daha kapsamlı hale getirir.Cihaz, sıvı ekranında test yöntemini, test kuvvetini, girinti uzunluğunu, sertlik değerini, test kuvveti tutma süresini, ölçüm sürelerini vb. görüntüleyebilen bir dijital ölçüm mikroskobu ile donatılmıştır ve bağlanabilen dişli bir arayüze sahiptir. bir dijital kameraya ve bir CCD kameraya.Yerli baş ürünlerde belli bir temsil gücüne sahiptir.
Test Cihazı-Direnç Dedektörü
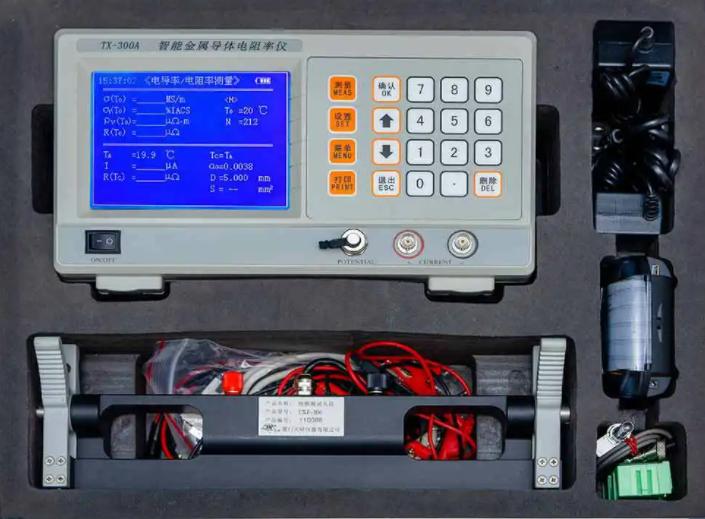
Metal tel özdirenç ölçüm cihazı, tel, çubuk direnci ve elektrik iletkenliği gibi parametreler için yüksek performanslı bir test cihazıdır.Performansı, GB/T3048.2 ve GB/T3048.4'teki ilgili teknik gereksinimlere tamamen uygundur.Metalurji, elektrik enerjisi, tel ve kablo, elektrikli ev aletleri, kolejler ve üniversiteler, bilimsel araştırma birimleri ve diğer endüstrilerde yaygın olarak kullanılmaktadır.
Enstrümanın ana özellikleri:
(1) Gelişmiş elektronik teknolojisini, tek çip teknolojisini ve otomatik algılama teknolojisini güçlü otomasyon fonksiyonu ve basit operasyonla birleştirir;
(2) Tuşa bir kez basmanız yeterlidir, ölçülen tüm değerler herhangi bir hesaplamaya gerek kalmadan sürekli, hızlı ve doğru tespite uygun olarak elde edilebilir;
(3) Pille çalışan tasarım, küçük boyutlu, taşıması kolay, saha ve saha kullanımına uygun;
(4) Büyük ekran, büyük yazı tipi, direnç, iletkenlik, direnç ve diğer ölçülen değerleri ve sıcaklığı, test akımını, sıcaklık telafi katsayısını ve diğer yardımcı parametreleri aynı anda görüntüleyebilir, çok sezgisel;
(5) Bir makine, iletken direnci ve iletkenlik ölçüm arayüzü, kablo kapsamlı parametre ölçüm arayüzü ve kablo DC direnç ölçüm arayüzü (TX-300B tipi) olmak üzere 3 ölçüm arayüzü ile çok amaçlıdır;
(6) Her ölçüm, her ölçüm değerinin doğruluğunu sağlamak için sabit akımın otomatik seçimi, otomatik akım değişimi, otomatik sıfır noktası düzeltmesi ve otomatik sıcaklık telafisi düzeltmesi işlevlerine sahiptir;
(7) Benzersiz taşınabilir dört terminalli test cihazı, farklı malzemelerin ve tel veya çubukların farklı özelliklerinin hızlı ölçümü için uygundur;
(8) 1000 set ölçüm verisi ve ölçüm parametresini kaydedip kaydedebilen ve eksiksiz bir rapor oluşturmak için üst bilgisayara bağlanabilen dahili veri belleği.